The Duravant family of operating companies serve the food processing, packaging and material handling segments.
Key Technology Introduces New ADR EXOS for Potato Strips
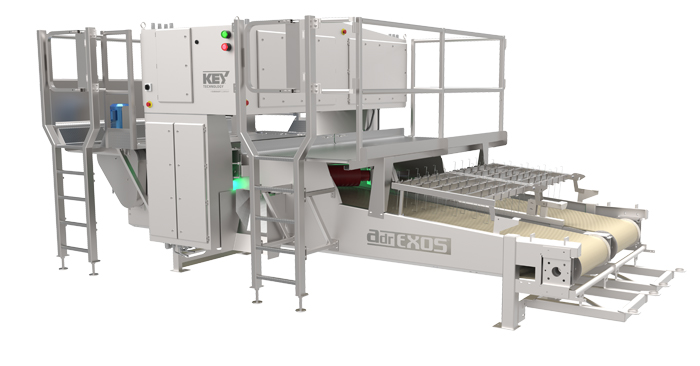
Key Technology, a member of the Duravant family of operating companies, introduces the newest automatic defect removal system for potato strips – ADR EXOS™ – at Interpom booth #257. As the only vision system on the market designed specifically to cut out defects from potato strips, ADR recovers French fries with defects and turns them into ‘good’ product, directly increasing yield. Featuring a new cutter-wheel design and intelligent software, the next-generation ADR EXOS better manages strip quality and length while improving product recovery to maximize process profitability.
ADR EXOS is available as a completely new system and as a field upgrade kit that allows existing ADR®5 users to access all the benefits of the new EXOS product technology.
“ADR EXOS offers an extremely fast payback. Processors new to ADR systems can recoup up to EUR €1,75 million worth of product per year with EXOS. Those upgrading from existing ADR5 systems to EXOS will improve their recovery value by as much as €150.000 per year,” said Marco Azzaretti, Advanced Inspection Systems Product Manager at Key. “Customers are telling us the quality of potato crops is becoming more variable due to challenging climate conditions. During seasons when processors risk not having enough good potatoes to meet demand, product recovery becomes even more critical. ADR EXOS is the ideal complement to wet potato strip digital sorting systems and a uniquely valuable tool to achieve the desired product quality at the highest possible yield.”
Building upon the field-proven technology of previous Key ADR systems, EXOS aligns, singulates, inspects and trims both peeled and peel-on wet potato strips of various cut sizes. The new cutter-wheel features even closer spacing between the air-actuated knives to more accurately place cuts closer to defects, which increases the average length of recovered strips.
ADR EXOS introduces a series of additional benefits, including a new knife retention system that eliminates the chance of unintended knife deployments, further improving product recovery and reducing maintenance. New intelligent software supports enhanced cut strategies, enabling more options for placing cut locations relative to each defect, including making multiple cuts on a single strip. Finally, a comprehensive smart diagnostics system continuously monitors knife cutting operations to detect any possible issues and ensure system performance remains consistent over time.
At production rates of up to 7.7 metric tons (17,000 lb.) per hour for shoestring cuts, and proportionally higher capacity rates for larger product cuts, ADR EXOS inspects defective potato strips that are rejected from an upstream digital sorter or all strips coming to it directly from the cutting equipment, depending on its location on the line. ADR EXOS can be used with Key’s recently-introduced VERYX® as well as Tegra®, Manta® and Optyx® strip sorting systems and competitive wet strip sorting systems. Key provides complete engineering support for combining sorting systems, ADR EXOS and Iso Flo® vibratory conveyors into complete integrated sorting systems.
For inspection accuracy, ADR EXOS relies on LED lights and high-resolution Vis/IR cameras to identify green and brown defects such as bruises and rot. The patented ADR belt conveyor and Iso-Flo® high-speed vibratory infeed conveyor accurately convey each potato strip for optimal inspection and trimming. To effectively handle a variety of strip types from shoestring to steak cut, ADR EXOS offers a “bed shift” capability so lane widths can be easily adjusted. The CleanBelt clean-in-place (CIP) system continuously removes starch from the ADR belt to prevent build-up, which improves sanitation, reduces labor, minimizes the cost of replacement parts and helps maintain optimal performance throughout the production cycle.
For more information on Key’s ADR EXOS, visit https://www.key.net/en/products/adr-exos/.
About Key Technology, Inc.
Key Technology is a global leader in the design and manufacture of automation systems including digital sorters, conveyors and other processing equipment. Applying processing knowledge and application expertise, Key helps customers in the food processing and other industries improve quality, increase yield, and reduce cost. Key manufactures its products at its headquarters in Walla Walla, Washington, USA; Beusichem, the Netherlands; Hasselt, Belgium; and Redmond, Oregon, USA. Key offers customer demonstration and testing services at five locations including Walla Walla, Beusichem, and Hasselt as well as Sacramento, California, USA and Melbourne, Australia; and maintains a sales and service office in Santiago de Queretaro, Mexico. Key is a Duravant Company.
About Duravant
Headquartered in Downers Grove, IL, Duravant is a global engineered equipment company with manufacturing, sales and service facilities throughout North America, Europe and Asia. Through their portfolio of operating companies, Duravant delivers trusted end-to-end process solutions for customers and partners through engineering and integration expertise, project management and operational excellence. With worldwide sales distribution and service networks, they provide immediate and lifetime aftermarket support to all the markets they serve in the food processing, packaging and material handling sectors. Duravant’s market-leading brands are synonymous with innovation, durability and reliability. Visit www.duravant.com.